How Predictive Maintenance is Revolutionizing Industries with AI
By AI Trends Editor
The combination of Artificial Intelligence (AI) and Internet of Things (IoT) sensors is transforming how companies approach maintenance. Predictive maintenance systems are proving to be one of the most successful AI use cases, helping businesses anticipate equipment failures and perform preventive actions before any significant breakdown occurs.
The Booming Predictive Maintenance Market
The predictive maintenance market, valued at $6.9 billion today, is projected to surge to $28.2 billion by 2026, according to a report from IoT Analytics of Hamburg, Germany. Currently, over 280 vendors offer predictive maintenance solutions, a number expected to grow to over 500 by 2026.
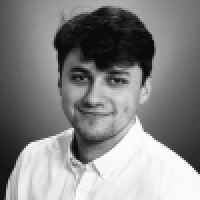
“This research serves as a wake-up call to those that claim IoT is failing. For companies owning industrial assets or selling equipment, now is the time to invest in predictive maintenance solutions,” stated Fernando Bruegge, author of the report. “Enterprise technology firms need to integrate predictive maintenance solutions into their offerings.”
Success Stories Across Industries
Aerospace: Rolls-Royce
Rolls-Royce has embraced AI-driven predictive analytics to reduce carbon emissions and optimize maintenance, allowing customers to keep planes airborne longer. By utilizing an Intelligent Engine platform, Rolls-Royce collects data on engine flights, weather conditions, and pilot behavior. Machine learning algorithms then customize maintenance regimes for individual engines, focusing on the engine’s actual condition rather than predefined schedules.

“We’re tailoring our maintenance regimes to optimize for each engine’s lifecycle, not just what the manual suggests,” stated Stuart Hughes, Chief Information and Digital Officer at Rolls-Royce. “It’s truly personalized maintenance, resulting in less service interruption.”
Healthcare: Kaiser Permanente
In healthcare, Kaiser Permanente has implemented predictive analytics to identify non-intensive care unit (ICU) patients at risk of rapid deterioration. The Advanced Alert Monitor (AAM) system analyzes over 70 factors from patients’ electronic health records to generate risk scores, enabling timely intervention.
Example: The AAM system has helped Kaiser Permanente significantly reduce unexpected ICU transfers, which though accounting for less than 4% of hospital population, represent 20% of all hospital deaths.
“The AAM system synthesizes vital statistics, lab results, and other variables to generate hourly risk scores,” stated Dick Daniels, Executive Vice President and CIO of Kaiser Permanente. “Remote teams evaluate these scores and notify rapid response teams to assess patients, allowing for timely interventions.”
Food Industry: PepsiCo’s Frito-Lay
At PepsiCo’s Frito-Lay plant in Fayetteville, Tennessee, predictive maintenance has dramatically reduced equipment downtime. The plant uses a range of monitoring techniques including vibration analysis, infrared analysis, and ultrasonic monitoring to preemptively address potential equipment failures.
Example: Vibration readings confirmed by ultrasound helped prevent a combustion blower motor failure, avoiding a shutdown of the entire potato chip department.
By leveraging these technologies, the Frito-Lay plant has minimized unplanned downtimes and maximized production efficiency, producing over 150 million pounds of product annually, including iconic brands like Lays, Ruffles, and Cheetos.
Manufacturing: Noranda Alumina
Automobile bearings often face wear under variable conditions, making them perfect candidates for predictive maintenance. At the Noranda Alumina plant in Gramercy, Louisiana, predictive maintenance has notably reduced bearing wear through improved lubrication systems, translating to significant cost savings.
Example: The implementation of predictive lubrication systems led to a 60% decline in bearing replacements, saving approximately $900,000 and preventing costly downtimes.
“Four hours of downtime results in about $1 million in lost production,” stated Russell Goodwin, Reliability Engineer at Noranda Alumina. “Our new lubrication system has enabled us to drop bearing changes by 60%.”
The Future of Predictive Maintenance
The rapid adoption and success of predictive maintenance across various industries underscore its vast potential. With AI and IoT technologies continually evolving, the integration of predictive maintenance solutions is set to become a standard practice, revolutionizing how businesses operate and maintain their assets.
As these examples illustrate, predictive maintenance not only prevents equipment failures and reduces downtime but also leads to significant cost savings and efficiency improvements. Companies that invest in these technologies now will be well-positioned to lead in their respective industries in the future.
What are your thoughts on the impact of predictive maintenance in your industry? Share your experiences and insights in the comments below!